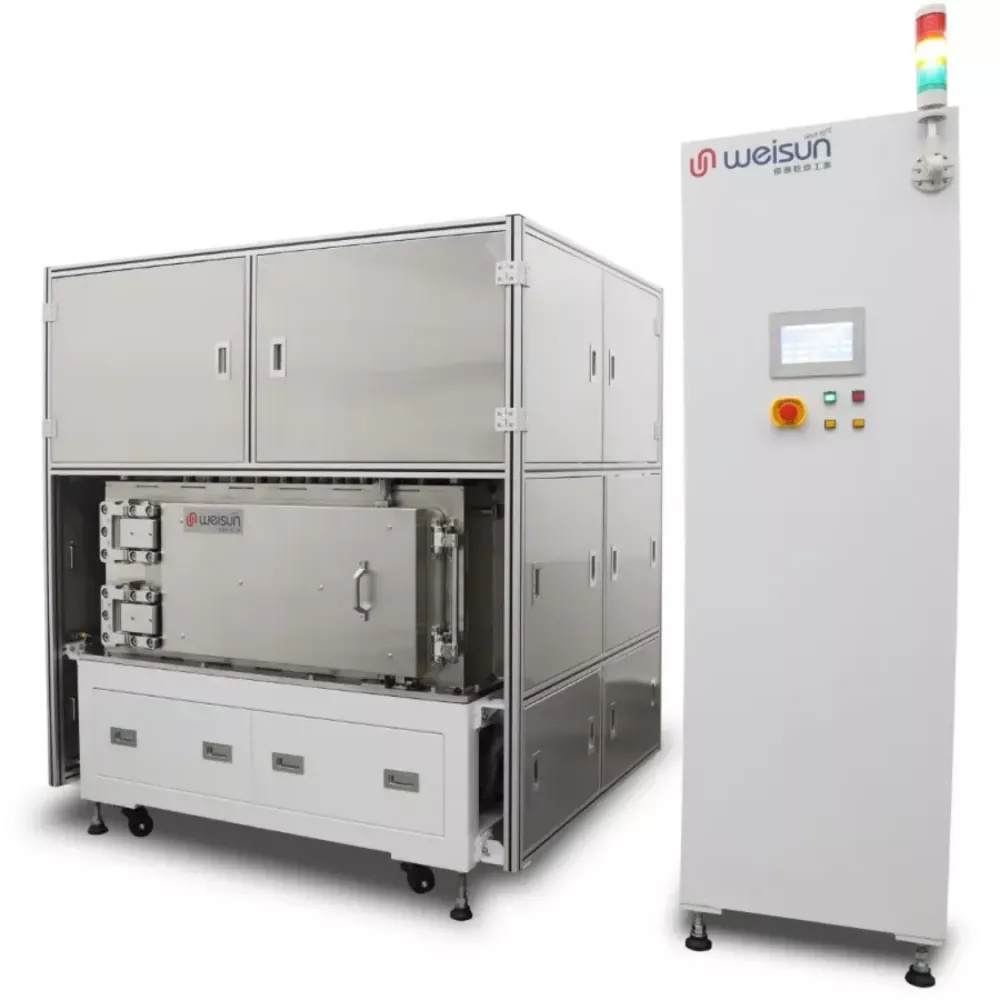
Vacuum IR Drying Equipment
The Best Solution for Semiconductor Drying and Curing Processes
Merchandise number:WIR-4-A01
Description:
- High-Performance Drying (Infrared IR)
- Energy Saving and Carbon Reduction
- Uniformity and Precision
- Reduced Oxidation Risk (Vacuum Environment)
- Control Capability (Process Flexibility)
Features Description:
High-Performance Drying (Infrared IR):
- Infrared radiation heats up quickly, reducing drying/curing time.
- Infrared's three key properties—penetration, reflection, and absorption—ensure excellent curing results for specific materials.
Energy Saving and Carbon Reduction:
- No need to heat the entire space; only the wafer surface is heated, reducing energy consumption.
- Compared to traditional hot air drying, energy consumption can be reduced by 30%.
Uniformity and Precision:
- Infrared penetrates materials for simultaneous internal and external heating, unlike hot air drying methods.
- Infrared wavelengths can be selected based on material properties to achieve optimal absorption.
Reduced Oxidation Risk (Vacuum Environment):
- Low oxygen levels in a vacuum environment prevent wafer oxidation during high-temperature processes.
- Superior bubble removal performance compared to atmospheric hot air ovens.
Control Capability (Process Flexibility):
- Multi-stage baking recipes and parameters with precise temperature and vacuum pressure control.
- 9-zone independent control system ensures uniform drying temperatures across all wafers.
Product Application:
Semiconductor Industry
Oven Specifications (PLC/PC Base)
↔️There is still information on the left and right.
Detailed Specifications | |
Process Temperature | Below 400°C (adjustable based on customer requirements) |
Temperature Uniformity | 150/250/390℃ ± 2% |
Heating Control Method | Infrared (IR) - Independent PID control for each zone |
Heating Rate | ≥8℃/min |
Cooling Rate | ≥6℃/min |
Average Cooling Deviation (U%) | Process Cooling Temp - 10%以下 |
Chamber Leakage Rate | 2x10-3 Pa*m3/sec |
Oxygen Level | None (optional detection module available for future installation) |
User Interface | User-friendly interface with Proface HMI Currently, the equipment does not support the following communication methods (optional for future customization): .CIM .Ethernet & SECS/GEM .PCB ECI |
Multi-Stage Process Control Settings | Supports multi-stage pressure and temperature control with PID modules |
Processes | The equipment can be applied to the following processes in the semiconductor industry: 1. Front-End Process: Photoresist (PI) baking and curing process. During the photolithography process, infrared drying can be used for rapid solvent removal from photoresist, ensuring uniformity and stability of the photoresist layer. 2. Back-End Process: Pre-packaging drying and curing. It can be used to cure adhesives, which helps improve packaging strength and reliability, enhances efficiency, and reduces defect rates. 3. Post-Cleaning Drying : After the wafer cleaning process, vacuum infrared drying technology can quickly remove moisture from the wafer surface. This helps improve the yield of subsequent processes and prevents moisture from affecting material adhesion. 4. Drying of Plastics and Resin Materials: In the packaging of certain semiconductor components, polymer materials (such as polyimide) need to be dried at high temperatures. Infrared drying technology effectively removes moisture from these materials. |