"Customization and high-end orders are our goals," said WEISUN General Manager Chen Wen-Han.
The journey from ODM to OEM in the traditional industry sector hasn't been easy. It required a shift in mindset, considering angles that the major players didn't want to explore and where smaller firms lacked research and development capabilities. Finding its own niche market was crucial. However, on the flip side, due to order customization instead of mass production, there's often a need for design changes. Furthermore, the surge in demand and component shortages after the pandemic has placed even more pressure on Wei Sheng's order delivery capabilities.
Supply chain disruptions and manufacturing process changes have resulted in a 60% increase in order delivery delays.
The production management department is responsible for aggregating production schedules. In the past, this was done using Excel to track procurement, inventory, and the actual progress on the shop floor. However, due to the numerous changes required for customized machinery, each work order corresponds to a unique process. If there are ten or even twenty work orders for the same machine, production management needs to modify the process flow twenty times.
Given the characteristics of the machinery equipment industry, the typical approach involves simultaneous contracting, design, and production. When design changes are needed, purchase orders and BOM change requests must be initiated, and designing while ensuring cross-functional communication becomes a significant challenge. On the procurement side, in the absence of a proper system, they often ended up chasing after materials, unable to perform effective cross-referencing based on machine models. This resulted in numerous checkpoints and a lot of time spent tracking and tracing materials.
"Before the introduction of project management and design change management, we relied on a whiteboard to track machine progress," said the Wei Sheng plant manager. Each machine has hundreds or even thousands of components, and in the past, it was necessary to confirm production progress with the machine department every day. After confirmation, personnel had to be scheduled, and production progress had to be reported.
In summary, the previous approach relied heavily on external personnel for control. Design and production were managed separately, updates relied on inquiries from production management. Additionally, the inventory situation was challenging to grasp, with procurement only starting to chase materials once they discovered shortages. Supervisors would report shortages when they noticed them. When design changes were required, they relied on manual comparisons with the BOM list, materials were issued from the warehouse after the fact, and additional materials were picked up by the warehouse after completion.
Project progress management and design change management are the solutions to unravel the complexities associated with multiple design changes in the process.
The implementation of project management and design change management systems has significantly reduced human errors at Wei Sheng, improving the efficiency of various functions. The system can generate various reports to assist in business analysis. Production management can now quickly grasp project progress before leaving work each day. They can also access progress through the system the next morning, eliminating the need for phone calls and on-site visits.
"I'm almost out of a job!" the production manager joked.
Design teams now need to report work progress daily, and the design change management system simplifies the content of their work. By maintaining BOM tables properly, they can respond to unforeseen events more effectively. Project control no longer requires waiting for project meetings, and they can check project progress "anytime, anywhere by opening their computers."
Previously, procurement had to locate all purchase orders, which often resulted in missed orders. With project progress management, they can cross-reference materials and inspection statuses using project numbers. The project management system directly presents data from ERP, reducing error and query times.
The plant management can now report machine progress through the critical path and task cards in the project management system, allowing them to see work schedules. Production management can also track progress without frequent on-site visits.
Efficiency has become the key to the success of project management, and the work value chain has shifted to be centered around people.
Chen Wen-Han highlights his expectations for WEISUN's digital transformation based on the benefits brought by this project. From informatization to digitalization and then to digital optimization, the goal is to "connect what people were doing with data and software."
Regarding project progress management, the current target for on-time project schedule achievement is 80%, ensuring that task schedules are met as planned. The on-time completion rate for critical tasks is estimated at 85%, with the on-time completion rate for assembly tasks raised to 90%. This is expected to increase the on-time completion rate of current machines by 43% and support a 45% improvement in on-time order delivery.
The changes brought by design change management enable the quick handling of new material requisitions and immediate handling of material tracing, reducing instances of material shortages. The processing time for dedicated material requisitions after a design change has been reduced from 4 days to 1 day, leading to a 50% reduction in dedicated material obsolescence. Communication for urgent handling of dedicated and old materials has lowered the risks and costs of obsolescence.
The efficiency improvement brought by project management, where software generates data, allows data to assist in decision-making, which Chen Wen-Han emphasizes as crucial for the future competitiveness.
What is clear is that the shift has gone from being task-centric to being "task finds the person," with a focus on people at the center.
WEISUN's office has transitioned from an old iron factory to a modern, spacious, and brightly lit environment with a contemporary light industrial aesthetic. The addition of an in-house gym reflects the company's aim to enhance work efficiency and employee well-being, giving staff more time for physical activity and building team cohesion indirectly.
From the production department to the establishment of various departments today, crossing the challenging barriers of transformation in traditional industries, the use of software tools to expand capacity has attracted the attention of domestic and international companies in the semiconductor, electronics, and optoelectronics industries. Orders are already scheduled into the middle of next year. With 46 years of history, Weisun is not only looking to maintain its position but also to innovate, explore new horizons, and further strengthen its competitiveness.

a high-ceilinged and minimalist reception hall
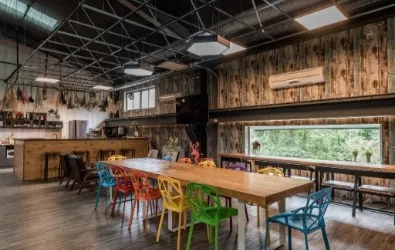
bright and spacious employee lounge area